SKU:710706
Amadesa
Máquina de Fundición Neutec® J-zF™ con Flowlogic®
Máquina de Fundición Neutec® J-zF™ con Flowlogic®
- Encabezado
- Encabezado
Precio habitual
$34,625.00
Precio habitual
Precio de oferta
$34,625.00
Precio unitario
/
por
|
Pre-order now! Estimated shipping date: 2025-09-13 |
No se pudo cargar la disponibilidad de retiro
La máquina de fundición por inducción Neutec® J-zF™ combina el tamaño compacto del J-zP™ con los beneficios de vanguardia y alta tecnología de la tecnología Neutec Flowlogic®. Esta máquina de fundición J-z con Flowlogic ofrece un sistema de fundición de joyería de alto rendimiento y costo efectivo para tu taller—ninguna otra máquina en este rango de precio se acerca en durabilidad robusta, bajo costo operativo y fundiciones de la más alta calidad. Los modelos J-z están diseñados para talleres de joyería de tamaño pequeño a mediano y ofrecen una impresionante gama de beneficios para tus procesos de producción. Configurada especialmente para la máquina de fundición J-z, la tecnología Flowlogic® ofrece una combinación exclusiva de innovadoras tecnologías nuevas. Flowlogic combina varios desarrollos en sistemas de control con un sistema dinámico de presión controlado por computadora integrado para proporcionar consistencia y flexibilidad a tus procesos de fundición que, hasta ahora, simplemente no eran posibles. La función Autocast™ del J-zF proporciona la conveniencia y precisión de la automatización a tu fundición. Cuando el metal alcanza el punto establecido, la máquina activa automáticamente la presión y el vertido—sin intervención del operador—en el momento óptimo para asegurar la mejor calidad posible en tus fundiciones. Debido a que el vertido está controlado de manera tan confiable, puedes fundir con éxito a temperaturas más bajas—ideal para procesos de fundición con piedra en su lugar. Las tecnologías Neutec Advanced Dynamic Computer™ (ADC) y Pulsed Power Stirring™ proporcionan la máxima simplicidad de operación—los tiempos de fusión más rápidos posibles y ciclos consistentes de fundido y vertido para cada aleación y cualquier tamaño de carga. La exclusiva Medida de Susceptancia Autodiagnóstica ajusta el desgaste del crisol variando la potencia y la frecuencia para un fundido óptimo cada vez.
• La programación adaptativa ADC™ ajusta automáticamente la potencia y la frecuencia miles de veces por segundo y mantiene un perfil metálico para cada metal que fundes, mejorando el tiempo y la precisión del perfil cada vez que fundes ese metal.
• El Pulsed-Power Stirring™ asegura fundiciones homogéneas y, con la programación Power Stir Cast, mantiene la aleación fundida completamente homogénea hasta el vertido—nunca tendrá que sobre-karatar para obtener valores consistentes en todo el árbol.Los moldes más grandes reducen el metal en proceso en un 20–25%, aumentan el número de componentes por fundición y ahorran tiempo en la línea de producción con superficies más suaves y menos defectos. En pruebas de producción, el ciclo promedio de fundición de molde a molde es de menos de tres minutos y medio—produciendo alrededor de 17 moldes por hora. Y los vertidos de 100 gramos se benefician del mismo programa de fusión preciso y eficiente que un vertido de capacidad completa.Los elementos de Flowlogic®:
• Sistema de diferencial de presión—Maximiza la presión sobre el molde en el momento más temprano posible al comenzar el vertido. Esto le permite bajar aún más las temperaturas del sistema para mejorar la calidad superficial, reducir la porosidad y aún así lograr la mejor tasa de llenado.
• Sistema Flowlogic® Tipo A—Un diseño innovador pendiente de patente que moldea el flujo del metal fundido, reduciendo la turbulencia y los vacíos aleatorios, y acelera la tasa de llenado a temperaturas más bajas, reduciendo la porosidad por contracción.
• Sistema cerrado—El metal se introduce en el crisol a través de una tolva cerrada. La cámara de fusión se inunda con gas inerte bajo presión positiva constante, eliminando el oxígeno del metal y forzándolo a subir y salir por la tolva.
• Sistema de alineación de moldes—Este sistema pendiente de patente asegura una alineación tan perfecta entre el molde y el crisol que el metal fundido logra consistentemente la "caída muerta" deseada hasta el fondo de su canal.
• NeuSprue® mejorado—Diseñado con un botón que reduce drásticamente la turbulencia en el punto de entrada, proporcionando un flujo de metal más suave y rápido, y una punta que retarda aún más la turbulencia donde comienza el llenado, estos canales están científicamente diseñados para optimizar la solidificación del metal.
• SuperPerf™ Flask—Con casi el 50% de sus superficies perforadas, estos moldes mejoran significativamente la desgasificación, mejorando mediblemente la tasa de llenado en cada molde probado.Otros beneficios:
• Componentes refrigerados por agua—La refrigeración interna con agua permite que el gabinete esté completamente sellado, minimizando el riesgo de daños causados por polvo o humedad.
• Panel de control digital fácil de usar—El centro de comando con pantalla táctil, fácil de ver y usar, pone el control al alcance de sus dedos.
• Reacción metal-a-inversión minimizada—Las temperaturas más bajas posibles gracias a Flowlogic® reducen las reacciones generadoras de gas que pueden crear defectos en las piezas fundidas.
• Altura ajustable—Ajuste los pies roscados de 65"H hasta 67"H según sea necesario para adaptarse a su espacio de trabajo y asegurar que la máquina esté perfectamente nivelada.
Ver todos los detalles
• La programación adaptativa ADC™ ajusta automáticamente la potencia y la frecuencia miles de veces por segundo y mantiene un perfil metálico para cada metal que fundes, mejorando el tiempo y la precisión del perfil cada vez que fundes ese metal.
• El Pulsed-Power Stirring™ asegura fundiciones homogéneas y, con la programación Power Stir Cast, mantiene la aleación fundida completamente homogénea hasta el vertido—nunca tendrá que sobre-karatar para obtener valores consistentes en todo el árbol.Los moldes más grandes reducen el metal en proceso en un 20–25%, aumentan el número de componentes por fundición y ahorran tiempo en la línea de producción con superficies más suaves y menos defectos. En pruebas de producción, el ciclo promedio de fundición de molde a molde es de menos de tres minutos y medio—produciendo alrededor de 17 moldes por hora. Y los vertidos de 100 gramos se benefician del mismo programa de fusión preciso y eficiente que un vertido de capacidad completa.Los elementos de Flowlogic®:
• Sistema de diferencial de presión—Maximiza la presión sobre el molde en el momento más temprano posible al comenzar el vertido. Esto le permite bajar aún más las temperaturas del sistema para mejorar la calidad superficial, reducir la porosidad y aún así lograr la mejor tasa de llenado.
• Sistema Flowlogic® Tipo A—Un diseño innovador pendiente de patente que moldea el flujo del metal fundido, reduciendo la turbulencia y los vacíos aleatorios, y acelera la tasa de llenado a temperaturas más bajas, reduciendo la porosidad por contracción.
• Sistema cerrado—El metal se introduce en el crisol a través de una tolva cerrada. La cámara de fusión se inunda con gas inerte bajo presión positiva constante, eliminando el oxígeno del metal y forzándolo a subir y salir por la tolva.
• Sistema de alineación de moldes—Este sistema pendiente de patente asegura una alineación tan perfecta entre el molde y el crisol que el metal fundido logra consistentemente la "caída muerta" deseada hasta el fondo de su canal.
• NeuSprue® mejorado—Diseñado con un botón que reduce drásticamente la turbulencia en el punto de entrada, proporcionando un flujo de metal más suave y rápido, y una punta que retarda aún más la turbulencia donde comienza el llenado, estos canales están científicamente diseñados para optimizar la solidificación del metal.
• SuperPerf™ Flask—Con casi el 50% de sus superficies perforadas, estos moldes mejoran significativamente la desgasificación, mejorando mediblemente la tasa de llenado en cada molde probado.Otros beneficios:
• Componentes refrigerados por agua—La refrigeración interna con agua permite que el gabinete esté completamente sellado, minimizando el riesgo de daños causados por polvo o humedad.
• Panel de control digital fácil de usar—El centro de comando con pantalla táctil, fácil de ver y usar, pone el control al alcance de sus dedos.
• Reacción metal-a-inversión minimizada—Las temperaturas más bajas posibles gracias a Flowlogic® reducen las reacciones generadoras de gas que pueden crear defectos en las piezas fundidas.
• Altura ajustable—Ajuste los pies roscados de 65"H hasta 67"H según sea necesario para adaptarse a su espacio de trabajo y asegurar que la máquina esté perfectamente nivelada.
- Dimensiones: 482.6 x 812.8 x 1701.8mm
- Voltaje: 208–240 voltios (monofásico)
- Amperaje: 50 amperios
- Frecuencia: 50/60Hz
- Capacidad: 200cc (líquido)
- Marca: Neutec
- Peso de envío: 562 lbs (254.919kg)
- País de Origen: Estados Unidos
- Peso: 254.919 kg
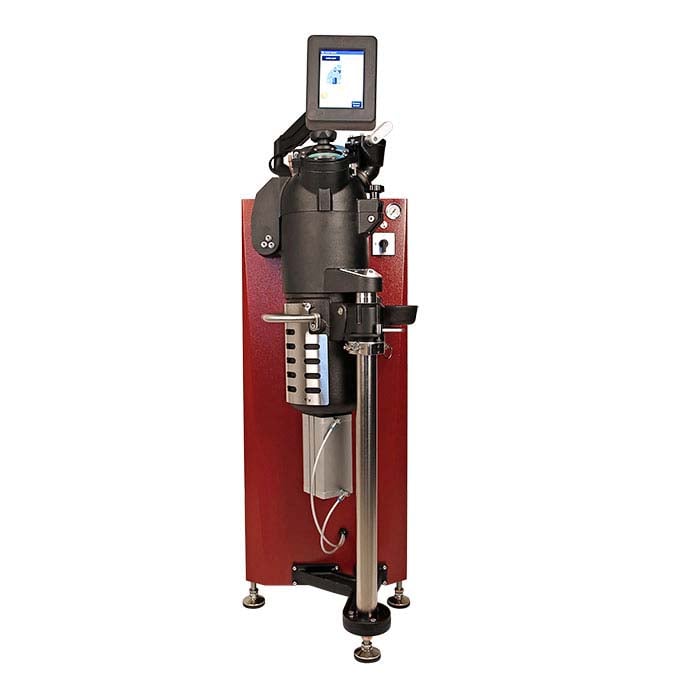
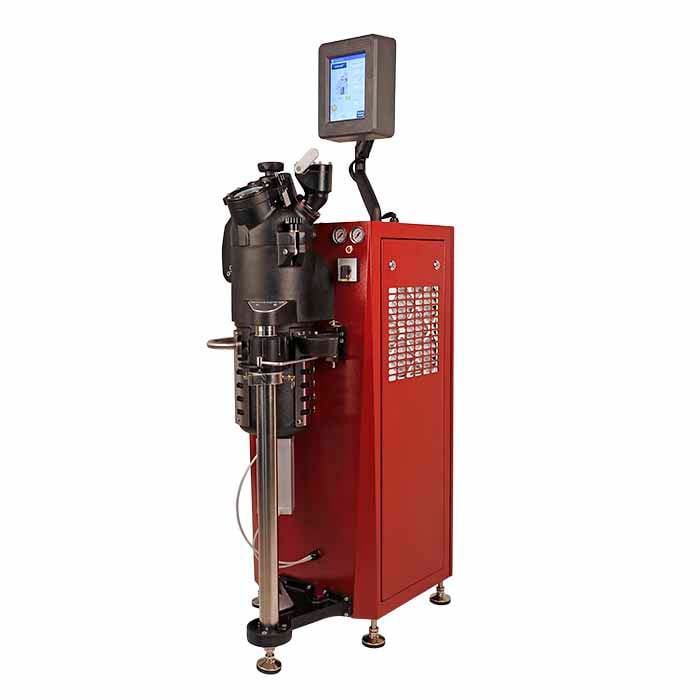
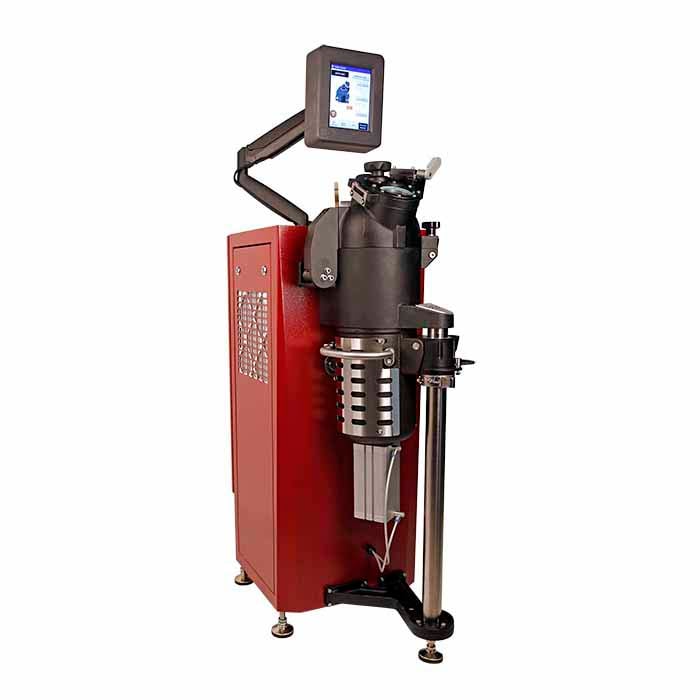